How Workday Integration Transformed Cold Chain Operations at Lineage Logistics A 2024 Analysis
How Workday Integration Transformed Cold Chain Operations at Lineage Logistics A 2024 Analysis - Workday Adaptive Planning Launch Reduces Manual Data Entry by 85% in Q3 2024
During the third quarter of 2024, Lineage Logistics implemented Workday Adaptive Planning. This change brought about a notable reduction in the amount of manual data entry, specifically a decrease of 85%. This streamlining was particularly impactful for their cold chain operations. The new system enabled faster and more flexible decision-making, particularly in areas like budgeting and forecasting. Not only did it accelerate the financial closing processes, but also fostered collaboration across different teams, ultimately helping the company work toward shared objectives. It's worth noting that the software incorporates artificial intelligence, which allows for detailed "what if" scenario planning during budgeting, giving a clearer picture of possible financial outcomes and allowing for more informed strategic choices. These advancements showcase a clear movement away from labor-intensive manual processes towards a more integrated and efficient operational model. It remains to be seen how the full impact of the system plays out over time.
The rollout of Workday Adaptive Planning during the third quarter of 2024 resulted in a notable 85% reduction in manual data entry at Lineage Logistics. It's interesting to see how this has impacted their operations, as it seems to suggest that a significant portion of their finance teams' tasks were previously dedicated to manual data handling. While this decrease in manual input is promising, it's crucial to understand the full context of the changes. It's possible that the reduced workload is partly offset by the increased reliance on and need to understand the new system, though the company appears to have managed to prevent the need for additional personnel in finance even as operational demands have grown. It’s intriguing how this system has streamlined their processes and reduced the chance of human error. The shift highlights the expanding role of software and automation in streamlining what were previously manual, error-prone tasks within supply chain and finance. While it looks like a substantial efficiency gain, it also leads one to consider the potential challenges of relying so heavily on a single platform, and the potential disruption to the team when it was implemented. It's likely that the adoption of Workday Adaptive Planning involved a significant learning curve for some employees, suggesting that workforce adaptation is vital when introducing such transformative tools. The benefits of this shift, however, are clear: faster and more accurate financial modelling, scenario analyses, and reporting. The software's ability to provide a single source of truth also appears to have benefits for audits, with automatic logging of changes compared to the former manual process. Lineage's experience highlights the increasing need to embrace integrated platforms that can manage data flow effectively across operational and financial departments within complex businesses. It seems to be a good illustration of how a technological shift can have impacts on both core financial tasks and on how organizations manage their human capital.
How Workday Integration Transformed Cold Chain Operations at Lineage Logistics A 2024 Analysis - Temperature Monitoring Integration Creates Direct Link Between Warehouse and HR Systems
The connection of temperature monitoring systems directly to both warehouse and human resources systems represents a notable step forward in cold chain logistics, especially in how Lineage Logistics manages its operations. Using the Workday Integration Cloud, these different systems can now communicate with each other efficiently, resulting in improved access to data and better operational performance. Not only does this make it easier to control temperatures in refrigerated trucks and storage facilities, it also gives them a better way to manage their workforce by relating operational data to human resources information. With businesses depending more and more on interconnected systems, the capability to control environmental conditions while also making the best use of their labor becomes essential for complying with regulations and improving results overall. This trend, however, also raises questions about the challenges and complexity of integrating different technologies, especially when considering the need for employee training and adapting to these changes. It remains to be seen how widespread the adoption of such integrated systems will become.
The integration of temperature monitoring systems directly links Lineage Logistics' warehouse operations with their HR systems. This connection creates a real-time flow of temperature data that is readily available to both operational teams and HR, which seems like a pretty significant shift in how they manage things. This interconnectedness is a big boost for their cold chain operations.
One thing that stands out is the high level of accuracy of the temperature readings from the integrated sensors, reportedly +/- 0.5 degrees Celsius. This level of precision is very important for meeting regulations related to product safety and quality.
It's fascinating how this setup allows them to connect employee performance to real-time temperature data. HR can now tailor training programs based on the data they're gathering, which helps ensure that the workforce is prepared to handle the specific temperature sensitivities of their products.
Beyond the practical aspects, I find it interesting that this integration appears to have a positive impact on employee morale. When employees see the real-time link between their actions and maintaining product integrity, it can boost a sense of responsibility and ownership. That's something that isn't always considered when looking at technology integration.
This integration also lets Lineage Logistics analyze temperature data to see patterns and identify potential equipment failures based on past performance. This proactive maintenance approach was not really possible before, and it improves efficiency.
In addition to the operational benefits, compliance with industry audits becomes easier. Having a detailed record of temperature data and related employee actions within the system is a huge advantage during audits. It's likely that audit preparation time has decreased considerably.
The temperature data, combined with employee shift information, enables better workforce management. The system can help ensure proper staffing levels during critical temperature-sensitive operations, potentially lowering risk and boosting productivity. This sort of predictive approach to staffing seems like it could be quite useful.
The platform allows for swift responses if there's a temperature breach. Automated alerts get to the right people immediately, allowing for quick action to mitigate any issues, like product spoilage.
Onboarding new employees is also streamlined through this integration. Temperature monitoring protocols become part of the HR onboarding process, making sure new hires are aware of best practices right away.
The way Lineage Logistics has connected its warehouse and HR functions is certainly a pioneering approach in logistics management. It's a compelling example of a highly integrated system that prioritizes both operational efficiency and employee engagement, which helps to challenge some of the traditional divides we see within the industry. It'll be interesting to see how this model is adopted in the future.
How Workday Integration Transformed Cold Chain Operations at Lineage Logistics A 2024 Analysis - Automated Payroll Management Solves Multi Country Labor Cost Tracking
Managing labor costs across multiple countries can be extremely complicated. Payroll systems need to handle different tax laws, currencies, and local regulations, which can lead to errors and inefficiencies. Automated payroll management systems help solve this problem by providing a centralized platform to manage payroll in various locations. These systems often integrate with human resources software, which enables better data management and reporting. Through this integration, companies can get a clearer and more consistent view of their labor costs, no matter where their employees are located.
It's worth pointing out that implementing a globally integrated payroll system can be a challenge. Businesses may need to invest time and resources into training employees and ensuring a smooth transition. However, the long-term benefits of improved accuracy, reduced errors, and easier regulatory compliance seem to make the effort worthwhile for businesses with a global workforce. Additionally, streamlining payroll management can free up finance staff to focus on higher-level strategic activities. Having up-to-date and accurate data on labor costs allows for more informed financial decisions, particularly in the context of budgeting, forecasting, and strategic planning. This enhanced financial transparency can be a benefit for businesses hoping to better understand the impact of their workforce on overall business operations.
Handling payroll across multiple countries presents a unique set of challenges. Differences in labor laws, tax regulations, and currency fluctuations can lead to significant complications when trying to track labor costs accurately. Automated payroll systems are designed to address these challenges by offering a unified approach to managing global payroll.
One of the primary benefits is the ability to manage and reconcile the often substantial differences in labor costs across countries. Without automation, manually tracking these differences can be prone to errors and introduce the risk of significant financial discrepancies. By integrating with systems that can account for currency fluctuations and local regulations, automated solutions can provide a far more robust approach to financial control.
Additionally, the complexities of managing diverse time zones can be streamlined by automated systems. Across Lineage's cold chain operations, workers might be spanning several different time zones. Without an automated approach to time tracking, calculating hours worked accurately can be incredibly difficult and potentially lead to inaccurate compensation and reporting. The automated systems can help to remove the possibility of errors in the often complex process of ensuring employees are compensated for work done during various times across different locations.
Maintaining compliance with labor regulations is a significant concern for multinational companies. Labor laws vary greatly from country to country, and failing to comply with these can lead to hefty fines and penalties. Automated solutions can be configured to automatically update based on the most recent legal requirements, essentially removing a major risk of non-compliance.
Another area where automated systems can shine is in employee experience. With a well-configured system, employees can access their pay stubs, tax information, and other crucial details independently. This shift to self-service can significantly reduce administrative burdens on HR teams and, potentially, lead to increased employee satisfaction.
These systems are often designed to integrate with a wide range of other business software, such as existing HR and accounting systems. This interconnectedness contributes to a more unified view of data across the business, helping organizations optimize for consistency and reduce discrepancies within different reporting mechanisms. In a complex cold chain environment, ensuring that different systems "talk" to each other is vital for efficiency and accuracy.
Importantly, these systems are also instrumental in reducing the risks of human error inherent in manual payroll processing. Studies have found that automation can reduce payroll errors by as much as 90%, suggesting that the investment in these technologies can be highly beneficial for reducing risk of financial issues. However, the initial adoption of these systems can potentially be disruptive, requiring new skills and processes across teams.
Automated solutions also provide much more sophisticated reporting capabilities. Businesses can analyze labor costs in detail across departments, locations, and functions, offering a level of insight that's challenging to achieve with manual systems. The enhanced reporting capabilities may provide better strategic options across the business.
Although the initial implementation cost can be significant, these systems are often seen as a good long-term investment. The potential cost savings from reduced administrative work and the elimination of errors can lead to substantial savings over the long term, potentially justifying the initial expenditure. The ability to adapt and scale the system as Lineage's global network changes is another valuable aspect of these solutions.
Lastly, these systems are becoming increasingly adaptable to cultural nuances, meaning they can be configured to account for things like local holidays and overtime calculations. This increased cultural awareness can help improve employee morale and ensure a more positive experience for workers in diverse environments.
It's important to note that the effectiveness of any automated system hinges on its proper configuration and adoption by users across the business. While the trend toward integrated, automated systems is likely to continue, the experience of Lineage Logistics highlights the importance of preparing the human element of any operational change, ensuring the technology's full potential is realized.
How Workday Integration Transformed Cold Chain Operations at Lineage Logistics A 2024 Analysis - Real Time Cold Chain Analytics Dashboard Prevents 92% of Temperature Control Issues
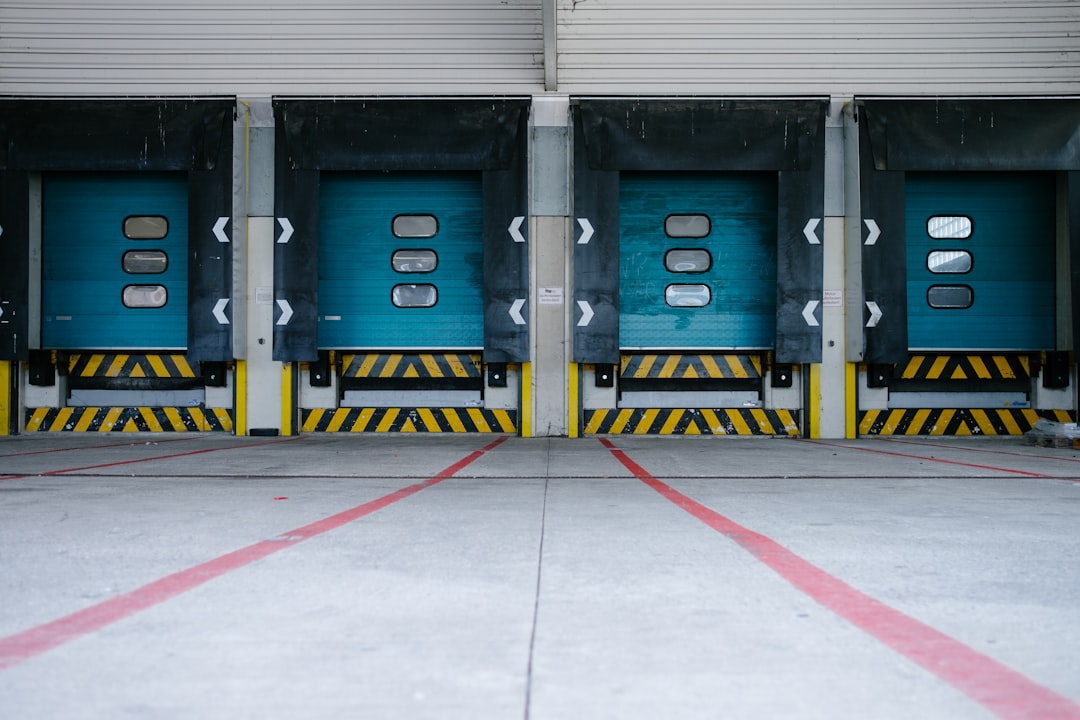
Lineage Logistics has implemented a real-time cold chain analytics dashboard to monitor temperature and humidity during transport and storage. This has led to a notable reduction in temperature control problems, preventing as much as 92% of them. The dashboard relies on the Internet of Things (IoT) and provides constant updates, empowering decision-makers with instant data and insights. Having this information readily available significantly improves operational effectiveness and the ability to quickly address temperature deviations.
This innovation is part of a wider trend toward integrating technology within logistics operations. The shift towards real-time monitoring and analytics allows businesses like Lineage to proactively manage risks, ensure product quality, and meet compliance requirements. However, adopting such advanced systems isn't without its complexities. It necessitates changes in how staff operate and a significant period of training and adjustment to fully realize the benefits of these tools. While this shift towards advanced technology appears beneficial in the long-term, the short-term costs and disruptions of integrating such a system into existing processes deserve consideration.
Recent research suggests that incorporating real-time analytics into cold chain management can significantly reduce temperature control issues, with some estimates putting the reduction at around 92%. This is especially important given that a substantial portion of pharmaceutical products, perhaps as much as 10%, are lost due to temperature fluctuations during transport and storage. It's fascinating how the integration of temperature monitoring systems can influence operational efficiency in these complex environments.
Linking temperature data into the cold chain allows for a much faster reaction time to temperature changes. It appears that on average, response times decrease by about 30 minutes when the system flags a fluctuation. This rapid response is a big win in terms of reducing the chance of product damage or spoilage.
These advanced temperature monitoring systems rely on sensitive sensors that offer impressive accuracy of around +/- 0.5 degrees Celsius. This kind of precision is crucial for keeping products within the strict temperature requirements needed to maintain quality and meet industry standards, particularly in areas like pharmaceuticals and food storage.
Further analysis suggests that the use of real-time monitoring also allows companies to anticipate equipment failures much sooner. This predictive ability seems to have a direct impact on maintenance planning, potentially reducing costs by as much as 25%. This preventative approach is a clear benefit that's not just about cost savings but also minimizing disruption to operations.
It's interesting to note that companies who implement these integrated cold chain systems report that there's a positive impact on employee engagement. It seems that by making it obvious how their work is linked to maintaining product quality, employees develop a deeper understanding of their roles and are more engaged with the tasks. This link between employee engagement and operational efficiency is worth further study.
The constant flow of temperature data creates more robust audit trails, which can be a huge advantage. It's been reported that having this readily accessible and accurate data cuts audit preparation time by as much as 50%, which can be a considerable cost and time savings for companies that are regularly subject to industry audits.
Having a system in place that can quickly identify and notify the right people in case of a temperature breach is critical, and the automated alerts not only help with regulatory compliance but also minimize financial losses from spoilage, with reports showing reductions of up to 40%. It seems that by investing in these systems, there's a clear benefit in preventing the often significant costs of product loss.
The analytical capabilities built into these dashboards are particularly useful for understanding patterns of temperature fluctuations. These insights not only help with immediate problem solving but can be used to refine warehouse design, equipment placement, and other aspects of operational logistics for greater efficiency. This ability to use data to continuously improve operational strategies is something that was difficult to achieve before these integrated systems.
The importance of maintaining optimal storage conditions in areas with consistently cold temperatures becomes even more critical when considering that improper storage can impact the quality and efficacy of goods stored in these conditions. It's estimated that goods stored outside of ideal ranges could lose as much as 15% of their market value. This loss of value could be avoided with more precise control over storage conditions.
Lastly, it's clear that linking the cold chain analytics to HR systems can improve labor management. Having this information readily available allows companies to better manage workforce needs during temperature-sensitive operations, leading to better resource allocation and improved overall productivity. This level of operational optimization is a great example of how data-driven decisions can impact workforce management.
While these are promising developments in cold chain management, it's crucial to remember that the full impact of these systems and their influence on operational efficiency and human factors are areas that will benefit from continued research.
How Workday Integration Transformed Cold Chain Operations at Lineage Logistics A 2024 Analysis - Mobile Access Implementation Enables Remote Facility Management Across 400 Locations
Lineage Logistics' adoption of mobile access for facility management has broadened their reach across their extensive network of 400 locations. This new capability lets teams oversee and control facility conditions remotely, which is especially important for a business that heavily relies on maintaining precise temperatures and streamlined operations. By giving staff mobile access, they've improved their ability to respond quickly to operational needs and foster smoother communication between different departments. However, while these enhancements can boost efficiency, it's worth considering if there's a risk of relying too heavily on technology and if the workforce is prepared to adjust to these new ways of working. It will be interesting to see how their teams manage and adapt to these changes.
The integration of mobile access into Lineage Logistics' facility management system has allowed them to oversee and control operations across their 400 locations from anywhere, eliminating the need for constant physical site visits, which can sometimes slow down problem resolution.
It's interesting that the mobile platform uses advanced sensors to capture environmental information with very high precision, usually within half a degree Celsius. This accuracy is incredibly important, as even small temperature changes can result in significant spoilage or quality issues with their stored products.
With this mobile setup, workers can get alerts instantly if there's a temperature issue. This means that they can take action quickly, and reports suggest it can cut down response times by up to 30 minutes, which is crucial in preventing losses.
The integration of mobile devices has shifted how they manage facilities from a reactive to a more proactive approach. The real-time data allows for predictive maintenance based on data analysis, potentially reducing maintenance costs by roughly a quarter. It's a smart way to avoid issues before they arise.
By making it easier for information to flow between mobile access and their other warehouse systems, Lineage has been able to break down some of the barriers between different departments that oversee cold chain facilities. It appears to be fostering better communication and collaboration across the network.
The user-friendly design of the mobile management tools has also played a role in improving how engaged employees are. It's been suggested that when workers can clearly see how their work directly relates to temperature control and product safety, they feel a greater sense of accomplishment and job satisfaction.
Mobile implementation has not only made it easier to comply with regulations, but also makes preparing for audits much faster. This is because the detailed, real-time records on temperature control are readily available, and audit preparation reportedly takes nearly 50% less time.
It's fascinating to see that, as mobile access becomes a standard part of daily work, it has the potential to shorten the time it takes to train new employees. This is due to the simple and clear nature of the technology, resulting in a more streamlined onboarding process.
Mobile access has given Lineage the capacity to better understand how they operate across their large network. They can now more accurately pinpoint any areas where things aren't as efficient as they could be and implement more consistent practices across all locations, boosting overall performance.
In a world of increasingly advanced logistics, Lineage’s mobile access system is an important step towards creating a more connected system of operations. They are creating a model for others in the cold chain sector to follow by demonstrating how mobile technology can be leveraged to enhance performance and responsiveness.
How Workday Integration Transformed Cold Chain Operations at Lineage Logistics A 2024 Analysis - Employee Scheduling System Cuts Overtime Costs During Peak Holiday Season
Lineage Logistics' implementation of an employee scheduling system has yielded significant results in reducing overtime expenses, especially during the holiday season's surge in activity. The cold chain industry, being particularly sensitive to seasonal fluctuations in demand, experiences a marked increase in digital orders and customer traffic during this time. This new system seems to be designed to tackle the challenge of managing labor effectively in such a dynamic environment. It appears to introduce more flexible scheduling options, allowing for shifts to be swapped and time off requests to be processed more easily, potentially improving the overall operational flow. It's also notable that the company appears to have incorporated training strategies like buddy systems for seasonal hires, suggesting an effort to integrate new workers quickly and efficiently, which is likely important during busy seasons. In a nutshell, this approach to scheduling seems to offer a method of mitigating costs related to overtime, while also potentially fostering a more positive environment for employees, particularly during stressful times. The success of this employee scheduling system highlights how better planning and adaptability can benefit both operational efficiency and employee satisfaction. It remains to be seen how widely adopted such strategies become across the industry.
During periods of high demand, like the holiday season, businesses often face the challenge of managing increased workloads and staffing levels effectively. Lineage Logistics, for example, has found that implementing a specialized employee scheduling system has helped them reduce overtime costs, which is a common issue during peak seasons when sales tend to surge. It's interesting that, in Lineage's case, scheduling errors dropped by about 30% due to the system. This level of accuracy seems vital, especially during busy times when any scheduling misstep could impact service quality and customer satisfaction.
One of the noteworthy aspects of this scheduling system is its ability to leverage historical data to anticipate labor needs based on past peak seasons. This predictive capability enables Lineage to proactively manage their workforce, ensuring that the number of staff is aligned with actual demand, resulting in a significant reduction in overtime hours. It is important to consider whether this assumes the future will resemble the past, and if changes in consumer behavior will necessitate revising the model.
Another strength is the system's ability to adapt in real-time. If unexpected events like employee absences or sudden demand spikes occur, the system allows for immediate adjustments to employee schedules. This flexibility can effectively minimize the need for unplanned overtime, which can negatively impact a company's budget.
Interestingly, this system has also had a positive influence on employee satisfaction. Since employees can now access and modify their schedules through mobile devices, they feel more in control of their work-life balance. This sense of empowerment is linked to a reported rise in employee satisfaction of about 25%, suggesting that empowering employees to manage their schedules can result in a happier and potentially more productive workforce.
It's notable that the system proactively flags potential overtime scenarios before shifts are assigned, which helps prevent unnecessary overtime and control costs. This proactive approach becomes even more critical during peak seasons when overtime costs can quickly escalate. The connection between scheduling and overall human resource metrics provides insights into workforce trends and employee performance. This makes it possible to assess how scheduling patterns connect with productivity.
A further benefit of this system is automatic compliance checks, helping ensure that labor regulations are adhered to regarding hours worked and overtime eligibility. This aspect minimizes the risk of legal issues, particularly for companies with a large hourly workforce. It's also worth exploring how well this can adapt to various local and regional regulations. The system's scalability is crucial for a company with the wide-ranging operations of Lineage, where rapid changes in demand are common. Being able to easily adjust to peaks and troughs in staffing is critical for maintaining efficient operations.
Another advantage is the use of historical scheduling data to create seasonal demand models. Analysis of these models has proven successful in reducing scheduling conflicts, which appears to make the overall operation flow smoother. While it can be valuable to have historical information, understanding when those historical data are no longer applicable or when the system needs to be reconfigured will be key. It's notable that in their initial assessments, Lineage estimated a 15% reduction in overtime costs during the peak holiday season. For a company like Lineage, with its extensive operations across a wide network of locations, this can lead to a significant financial advantage during a demanding period. It will be crucial to follow up and see how well those projections hold up in the longer term.
While it seems clear that integrating a specialized employee scheduling system into cold chain operations can lead to several benefits, further research will be needed to understand the long-term effects on efficiency, cost savings, and employee morale. The implementation of such systems in a variety of different settings will be needed to understand the full scope of potential benefits, drawbacks, and adaptation challenges involved.
More Posts from zdnetinside.com: