7 Essential Tech Tools Reshaping Field Service Technician Workflows in 2024
7 Essential Tech Tools Reshaping Field Service Technician Workflows in 2024 - Mobile Field Service Apps with Offline Capabilities Connect Remote Teams
In today's increasingly distributed workforce, mobile field service apps that work offline are essential for keeping remote teams connected and productive. Many field service technicians operate in areas with spotty or no internet access, making offline functionality a necessity. These apps provide access to critical data and tools, enabling technicians to complete tasks even when they're out of range of a network.
Features such as offline data synchronization and access to previously downloaded data are paramount for these tools. They are a game-changer for those who operate in remote regions or where connectivity is intermittent, such as in construction, utilities, and industrial maintenance. These types of apps promote autonomy and efficiency for technicians, reducing reliance on continuous network connections. They can also facilitate real-time decision-making in situations where connectivity drops, optimizing resource allocation and potentially preventing delays.
However, it's crucial that these tools are well-designed. If the offline data storage isn't robust enough or if the synchronization process is problematic, it can create headaches and ultimately lead to less efficient workflows. Despite the advantages, there are still limitations and trade-offs that need to be addressed, like ensuring seamless data syncing and managing the potential for data conflicts when online. But the overall benefit of these tools is clear: connecting and empowering remote teams even in areas lacking reliable internet access.
In the realm of field service, where technicians often operate in remote or challenging environments, the ability to maintain productivity without a constant internet connection is crucial. Mobile field service applications with offline capabilities have become indispensable tools, allowing technicians to access critical information and complete tasks even in areas with spotty or no connectivity.
These apps typically leverage local storage, caching essential data like work orders, parts lists, and customer information directly on the device. This approach reduces reliance on network connectivity, thereby minimizing delays and ensuring a seamless workflow. The advantage of this offline mode is quite clear—technicians can continue to operate, complete tasks, and even perform diagnostics, without having to wait for an internet connection.
Moreover, the ability to sync data once a connection is re-established prevents data loss, a critical factor in maintaining operational efficiency. Several providers, including Oracle and Microsoft, offer such solutions integrated with their broader enterprise resource planning (ERP) or customer relationship management (CRM) systems. Some solutions, like Resco, are built with an "offline-first" philosophy, prioritizing seamless functionality even in the absence of an active network connection.
This offline functionality is particularly valuable in sectors like construction and utilities where work locations can be remote, and service calls might need to be addressed urgently. It's worth noting that the benefits extend beyond just maintaining productivity; features such as offline mapping and machine learning-driven diagnostics can be leveraged for better route optimization and proactive maintenance decisions.
However, a critical consideration is the security implications of storing sensitive information locally. Robust encryption and data management practices are essential to safeguard the integrity of data stored on mobile devices. While the advantages of offline access are significant, developers and businesses must prioritize security to mitigate the risks associated with handling sensitive information in a disconnected environment. Ultimately, the adoption of mobile field service apps with offline capabilities reflects the evolving nature of field service, where operational efficiency and the ability to operate in diverse conditions are paramount.
7 Essential Tech Tools Reshaping Field Service Technician Workflows in 2024 - Smart Glasses and AR Tools Transform Equipment Diagnostics
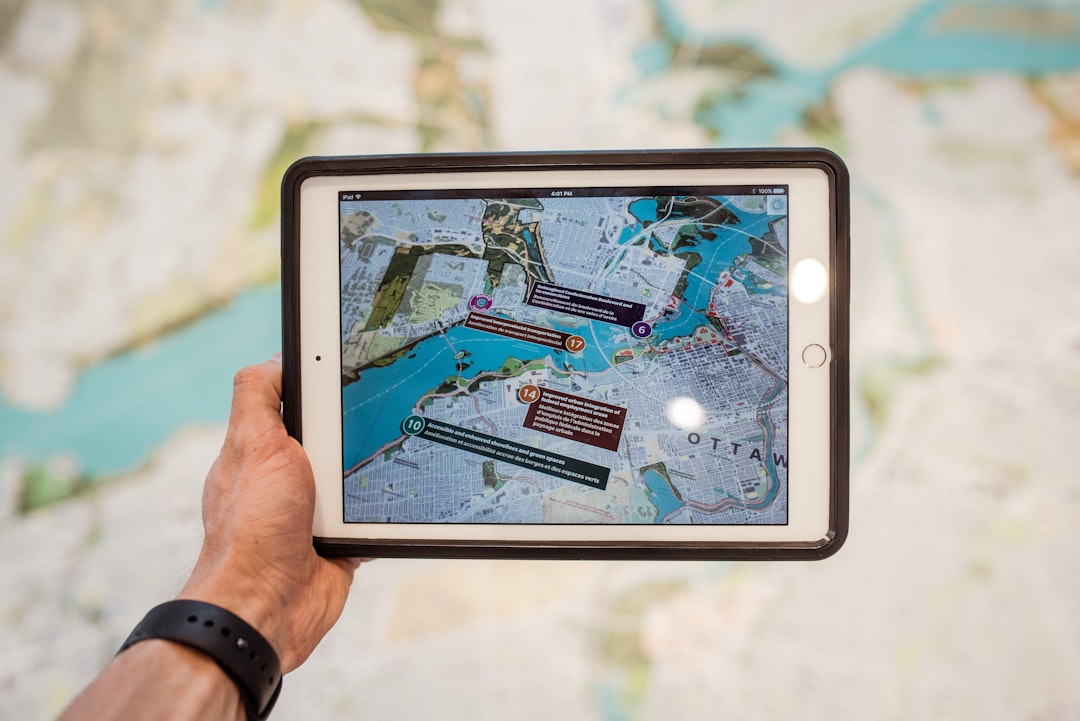
Smart glasses and augmented reality (AR) tools are increasingly transforming how equipment diagnostics are handled in field service. These technologies overlay digital information, like instructions and 3D models, directly onto a technician's view of the equipment. This hands-free approach allows technicians to work more efficiently while also minimizing errors that can stem from fumbling with manuals or relying on memory. The integration of AR provides real-time contextual information, leading to fewer mistakes and potentially enhancing safety on the job site.
Moreover, the ability to connect with remote experts via these smart glasses can drastically improve diagnostic accuracy and speed up repairs, potentially reducing travel times for both experts and technicians. It's a powerful tool for collaboration, especially when dealing with complex or uncommon issues. While the benefits are apparent, the integration of AR into existing workflows can present challenges. Training technicians on new hardware and software is crucial, and there's the possibility of encountering compatibility issues with certain systems. Despite this, it's clear that AR tools are poised to disrupt the traditional methods of diagnosing and repairing equipment, ushering in a new era of efficiency and effectiveness in field service operations.
Smart glasses and augmented reality (AR) tools are becoming increasingly important for equipment diagnostics in field service. These devices are essentially wearable computers that can overlay digital information onto the real world, providing technicians with real-time insights during repairs and maintenance. One of the most promising aspects of this technology is the ability to provide hands-free access to data. Instead of constantly referencing manuals or tablets, technicians can see instructions, diagrams, and even 3D models of components directly on the equipment, overlaid through their glasses.
However, these tools are not without their learning curve. Both the hardware and software interfaces require thorough training for effective use, especially for technicians not used to this type of interaction. Even with training, the human-computer interaction can sometimes be clunky and distracting. The promise of increased efficiency rests heavily on this smooth interaction.
Beyond simply viewing data, AR in smart glasses opens up new possibilities for remote assistance and collaboration. Experts located anywhere can see through the technician's eyes, effectively providing real-time guidance during troubleshooting. This remote expertise is especially beneficial in situations where specialized knowledge is required or when sending a technician on-site is costly or time-consuming. It has the potential to significantly reduce the need for travel, which translates into faster resolution times and improved technician utilization.
Interestingly, the combination of AR and image recognition has the potential to further streamline diagnostics. The technology can potentially identify components and automatically suggest potential repair paths based on its knowledge base. While this technology is still relatively new, it holds promise for improving accuracy and reducing errors during inspections.
Another interesting area is the integration of AR into training programs. By overlaying training materials directly onto the equipment, technicians can learn complex procedures in a more engaging and intuitive way. This could lead to a more skilled and prepared workforce and hopefully improve the speed and efficiency of field service repairs.
However, the rapid evolution of AR technologies also introduces considerations about data security and integration with existing enterprise systems. Ensuring data privacy and ensuring seamless integration are key challenges that developers and organizations are constantly working to overcome.
It is still early days in the broader adoption of AR tools in field service. Although there are obvious potential benefits such as enhanced collaboration, faster resolution times, and reduced travel, it will take time for the technology to mature and for workflows to be fully optimized to take advantage of these capabilities. But the concept of having real-time visual data readily accessible to field technicians in the midst of complex repairs has the potential to transform the field service landscape. The future of field service may well be one in which every technician has a set of smart glasses that are a constant aid to making sure that tasks are completed correctly and safely.
7 Essential Tech Tools Reshaping Field Service Technician Workflows in 2024 - AI Powered Scheduling Software Cuts Response Times by 40%
AI-driven scheduling software is significantly improving the speed and effectiveness of field service operations by reducing response times by as much as 40%. This technology essentially automates the scheduling process, allowing teams to allocate resources and plan work orders with greater precision. By intelligently analyzing factors like technician availability, travel times, and service needs, these tools can prevent over-scheduling and ensure that technicians are deployed where they are needed most, when they are needed. This helps minimize wasted time and ensures that service requests are addressed promptly.
These advancements aren't just about quicker scheduling. By handling much of the administrative burden of planning and assignment, technicians can dedicate more time to core tasks. Additionally, these scheduling programs often seamlessly integrate with existing calendar and task management systems, promoting a unified approach to time management that fosters smoother and more efficient workflows. While the integration of AI into scheduling is relatively new, it's clear that it has the potential to streamline field service and improve service delivery by optimizing technician time and minimizing delays. However, it's important to evaluate these tools carefully to see if they genuinely optimize existing workflows or create new challenges that need to be managed.
In the evolving landscape of field service, AI-powered scheduling tools are demonstrating a notable impact on operational efficiency. Researchers have observed that these intelligent systems can significantly decrease response times, with some studies suggesting a reduction of up to 40%. This efficiency gain stems from the software's capacity to analyze vast amounts of data, including historical trends, technician availability, and even real-time traffic conditions. By leveraging this data, the software can optimize appointment scheduling and technician routes, minimizing travel time and maximizing the number of jobs completed within a given timeframe.
While this technology seems promising, there are potential drawbacks to consider. The algorithms used by AI scheduling software are trained on existing data, and if that data contains inherent biases or reflects historical inefficiencies, the AI may perpetuate those issues in its scheduling decisions. This means that continuous monitoring and fine-tuning of the AI's training data are crucial to ensure optimal outcomes. Further research is needed to understand the potential impact of algorithmic bias on scheduling decisions and overall fairness.
It's also important to recognize that the effectiveness of these systems depends on the quality and quantity of data used to train them. If a company's data is incomplete or poorly structured, the AI may struggle to make accurate predictions or generate efficient schedules. The integration with other systems, such as those related to inventory management, can be essential for the accuracy of the scheduling decisions. These tools also need to be considered carefully within the context of a business's overall data security infrastructure and practices.
However, the potential advantages of AI-driven scheduling seem undeniable. By automating certain aspects of scheduling, such as appointment booking and route optimization, the software can free up human dispatchers to focus on more complex or nuanced tasks. It can also reduce the risk of human error in scheduling, such as double-booking technicians or assigning jobs without considering the availability of required parts. While the technology is still evolving, initial results suggest that AI scheduling has the potential to reshape field service operations, making them faster, more efficient, and possibly more responsive to customer needs.
7 Essential Tech Tools Reshaping Field Service Technician Workflows in 2024 - IoT Sensors Enable Real Time Equipment Monitoring
In the field service landscape of 2024, the use of IoT sensors for real-time equipment monitoring has become increasingly important. These sensors, embedded in various machines and infrastructure, provide a continuous flow of data about operational conditions like temperature, pressure, and vibration. This constant stream of information gives technicians a detailed picture of equipment health, allowing them to identify potential issues before they cause major problems. This proactive approach to maintenance, often called predictive maintenance, can prevent unexpected failures and reduce downtime, minimizing disruption to operations and ultimately saving businesses money.
The ability to monitor equipment remotely in real-time through IoT also extends to things like energy and resource management. In industries like manufacturing and utilities, IoT sensors provide a way to optimize resource use by tracking factors like energy consumption and water usage. This can lead to improved efficiency across a range of operations. While the advantages of IoT in this field are numerous, we should be mindful that this constant flow of data introduces new challenges. The sheer volume of data generated can create a significant storage and management burden for businesses, and concerns around data security need to be addressed carefully. With data potentially containing sensitive information about equipment and operational procedures, robust security protocols are needed to ensure it is protected from unauthorized access. Overall, while IoT sensors introduce a powerful capability for improving the efficiency of field service operations and equipment management, there are potential downsides and tradeoffs to consider that need thoughtful planning. We are likely to see increased adoption and integration of these sensors within the industry, but as with any new technology, it's important to balance the benefits with the challenges involved.
In the ever-evolving field of equipment maintenance and monitoring, the Internet of Things (IoT) has emerged as a pivotal technology. At the core of many IoT applications are sensors, tiny devices that gather data about the surrounding environment and relay it to a central system for analysis and action. These sensors, it turns out, have a remarkable capacity to provide real-time insights into the health and performance of equipment. It's amazing how much these small devices can do!
The sheer speed at which some of these sensors operate is astonishing. We are talking sub-millisecond response times in some cases, meaning that if an anomaly arises, technicians can almost instantaneously be alerted. However, this capability comes at a cost: data volume. An individual sensor can produce tremendous amounts of data—upwards of 25 gigabytes a day in some instances. This volume of information might seem overwhelming, but it's within this wealth of data that opportunities for understanding long-term equipment trends and establishing more effective predictive maintenance programs lie.
Moreover, the versatility of modern sensors is truly impressive. These sensors don't just capture one piece of information; many are capable of monitoring multiple aspects of an environment or piece of machinery simultaneously. Temperature, pressure, vibration—you name it, there's a sensor for it. The potential for gaining a far more holistic picture of equipment health is remarkable with this capability.
It's not just about data collection; many IoT sensor designs allow technicians to manipulate settings remotely. This capacity to configure sensors from afar can translate to quicker diagnostics and reduced downtime for the equipment. Perhaps even more remarkable, many of these sensors now comply with standardized communication protocols, which means they can seamlessly integrate with other systems. This creates flexibility for businesses to design equipment monitoring systems that best suit their needs, without being locked into particular vendor solutions.
In addition to their standard capabilities, researchers have explored the use of machine learning algorithms alongside sensor data. In some applications, these machine learning approaches are analyzing sensor data trends and have the potential to offer predictive insights that might assist technicians in anticipating and preventing equipment failures. Even more intriguing is the fact that some sensor designs are exploring energy harvesting technology. This potentially removes the need for battery replacements or ongoing energy management for the sensors, which simplifies maintenance even further.
A few other aspects of IoT sensors bear consideration. Because they are connected devices, they frequently receive over-the-air updates. This capability means the sensor software and security features can remain current without any physical interaction with the sensor, a huge advantage in remote applications. The same connected nature also allows for the inclusion of more robust safety protocols. In certain scenarios, they can instantly trigger alerts or shutdowns if potentially dangerous conditions are identified, thereby enhancing workplace safety. Lastly, and this is a notable technological development, researchers are exploring how data can be processed directly on the sensor instead of transmitting all the data back to a central location. This edge processing capability has the potential to reduce latency and make the entire system much more responsive.
It's clear that IoT sensors are a key technology for future equipment maintenance and monitoring activities. With the ongoing innovation in the field, we can anticipate that the capabilities of these devices will continue to evolve rapidly, providing even more valuable insights for field service operations. They will likely become increasingly integrated into workflows and continue to have a far-reaching impact on equipment management practices for years to come.
7 Essential Tech Tools Reshaping Field Service Technician Workflows in 2024 - Digital Knowledge Base Systems Speed Up Problem Resolution
Digital knowledge bases are changing the way field service technicians solve problems. They help customers find solutions on their own, reducing the need for immediate human interaction and leading to faster resolution times. These systems also make internal processes more efficient, helping onboard new technicians faster and boost overall team productivity.
Tools like Freshdesk and Confluence are widely used to maintain up-to-date information, putting vital resources at technicians' fingertips. But, to reap the full benefits, it's important to consistently update and check the accuracy of the information in a knowledge base. If the content isn't kept current, the whole system can become unreliable and lose its effectiveness for support tasks. It’s a balancing act between the promise of efficient workflows and the reality of managing the information within the system. While the potential for improved efficiency and knowledge sharing is clear, the success of these systems hinges on careful management and upkeep.
Digital knowledge base systems are increasingly becoming essential tools for field service technicians, especially as the complexity of equipment and the need for rapid problem resolution continue to rise. These systems act as centralized hubs of information, offering immediate access to technical documentation, troubleshooting guides, and best practices.
The benefit of having this information immediately available is substantial. Technicians no longer have to spend valuable time searching through manuals or relying on memory. Instead, they can quickly retrieve the precise knowledge they need to diagnose and resolve problems, often leading to a substantial reduction in resolution times—studies have shown reductions of up to 50% in some cases. This speedier problem solving translates into faster turnaround times for customers, reducing frustration and increasing overall satisfaction.
Furthermore, these knowledge bases aren't static. Many utilize machine learning to adapt and improve over time. As technicians add their own solutions and insights, the system becomes more intelligent, learning from past experiences and predicting potential solutions to frequently encountered issues. This continuous learning capability helps standardize practices, ensuring that all technicians follow established procedures. This standardization fosters consistency in problem-solving approaches, thereby enhancing the uniformity of service quality.
However, one challenge is ensuring that the knowledge base is continuously updated and remains relevant to the ever-changing world of field service technology. As new equipment and procedures are introduced, it's essential for the systems to be readily adaptable to integrate the new knowledge. This dynamic nature of the knowledge base is vital in fast-paced environments.
Another aspect of these systems is their potential to facilitate collaboration. Several digital knowledge bases include integrated tools that enable technicians to share solutions, experiences, and insights in real-time. This shared knowledge fosters a culture of continuous improvement and helps to reduce the knowledge gaps that can occur when technicians have varying levels of experience. It also helps avoid the development of information silos, where vital troubleshooting techniques and insights are isolated within individual teams or technicians.
Beyond basic documentation, these systems can integrate with other advanced tools being used in the field. Integration with AR tools and IoT sensors offers technicians real-time situational context combined with knowledge base information for making more informed and timely decisions. The potential for integrating sensor data with knowledge bases has interesting implications for predicting potential equipment failures, allowing technicians to implement preventative maintenance strategies that save time and reduce the likelihood of costly breakdowns.
The design of these systems also plays a crucial role in their overall usefulness. An intuitive and easy-to-navigate interface can ensure that technicians of varying technical abilities can quickly and effectively find the information they need. This focus on user-friendliness is important for maximizing the effectiveness of the system.
As we move forward, we'll likely see continued refinement of digital knowledge base systems. The goal is to create even more effective tools to support technicians and improve customer satisfaction by enabling the rapid resolution of problems on the first visit. This capability not only saves time and reduces costs but also fosters strong relationships with customers. The future of field service will depend increasingly on leveraging readily available, accurate information to enhance technician skills and solve problems quickly and efficiently.
7 Essential Tech Tools Reshaping Field Service Technician Workflows in 2024 - Automated Invoice and Payment Processing Reduces Admin Time
Automating invoice and payment processing is transforming how field service businesses handle their finances. Tools that use technologies like Optical Character Recognition (OCR) and Robotic Process Automation can automate tasks like data extraction from invoices and payment approvals, reducing the need for manual data entry and human error. This automation is becoming increasingly common, with a significant number of businesses, particularly mid-sized ones, now using it for tasks related to accounts payable and receivable.
The benefits can be substantial. Studies suggest that automation can free up administrative teams, like accounts payable (AP), by more than 10 hours each week. This increased productivity also translates to potentially lower labor costs and a smoother workflow for financial operations. Overall, it's becoming a critical component for businesses seeking to modernize their processes and lessen the burden of manual administration.
However, successful implementation and ongoing management are key. While the technology shows promise, careful planning and ongoing maintenance are still needed to avoid any unforeseen challenges. It's important to consider that the benefits of automation, while compelling, are dependent on effectively integrating the tools within a company's existing systems and workflow.
In the context of field service workflows in 2024, automated invoice and payment processing is increasingly being recognized as a vital tool for improving efficiency. While field technicians are primarily focused on providing service, the associated administrative tasks, particularly invoicing and payments, can often be a major drain on time and resources. Automating these processes can lead to a substantial shift in how resources are allocated.
One notable aspect is the reduction in errors that automated systems can achieve. Manual data entry in traditional invoicing processes is prone to human error, which can lead to billing inaccuracies, delays, and even potential fraud. Optical Character Recognition (OCR) technology, for example, is used in some systems to automatically extract data from invoices, minimizing the potential for these errors. Reports indicate that some companies have seen a drastic reduction in invoice errors—from over 20% down to less than 1%—after implementing these automated systems.
Furthermore, automated invoice processing can significantly reduce the time spent on administrative tasks. By automating things like data entry, invoice verification, and payment processing, organizations can free up administrative staff to focus on other crucial tasks. Studies show that AP teams using automated systems can save upwards of 10 hours per week, resulting in increased productivity and reduced labor costs.
However, there are complexities to consider. The integration of these systems into existing workflows can sometimes be challenging. If a company is using multiple, disparate software systems for accounting and billing, connecting them to an automated invoice system might require significant adjustments to the current infrastructure. Additionally, these systems are often dependent on consistent, structured data for optimal performance. If data isn't consistently formatted or contains inconsistencies, the automation might not work as intended, potentially leading to new problems.
Another aspect that needs consideration is the potential for software integration issues. Ideally, automated invoice systems can integrate with Enterprise Resource Planning (ERP) systems, which streamlines information flow and improves overall efficiency. But if the integration isn't well-designed or if the ERP system isn't compatible, the integration can be difficult to implement or may result in data conflicts. This highlights the need to carefully evaluate compatibility before implementing an automated system.
Looking ahead, the trend towards automating invoice and payment processing is likely to continue. Organizations are increasingly recognizing the benefits of reduced administrative overhead, improved accuracy, and faster payment cycles. While some challenges remain, like ensuring data accuracy and seamless integration with existing systems, the overall benefits of automated invoice and payment processing are compelling. For field service operations seeking to optimize their financial workflows and reduce the administrative burden on their teams, this technology is proving to be quite beneficial.
7 Essential Tech Tools Reshaping Field Service Technician Workflows in 2024 - Advanced Route Optimization Software Minimizes Travel Time
Advanced route optimization software is becoming increasingly important for field service technicians, primarily because it helps reduce travel time. These tools often use artificial intelligence to map out the most efficient routes for technicians making multiple stops, taking into account things like delivery timeframes, specific service needs at each location, and even the capacity of the vehicles. This approach has the potential to reduce wasted time spent driving between appointments and cut down on things like fuel usage and wear and tear on vehicles. The net effect is that these tools help field service teams improve overall efficiency.
Keeping these routes optimized requires constant monitoring and updates, especially with real-time traffic or other unexpected delays that can affect travel times. These software tools need to be able to incorporate up-to-the-minute information to ensure routes remain efficient. The promise of such tools is clear, but businesses need to be thoughtful in implementing them. These tools can introduce their own set of complexities, and it is not always obvious that using them will improve the workflow. Simply adding a new software tool isn't always a path to greater efficiency. There are many aspects of integration and data management that need to be carefully thought out before these tools are adopted.
In the dynamic landscape of field service, advanced route optimization software is emerging as a key player in minimizing travel time for technicians. These sophisticated tools leverage a variety of techniques to streamline the process of planning and navigating routes, ultimately leading to quicker service delivery and improved customer satisfaction.
One of the most noteworthy aspects of these advanced tools is their ability to adapt to real-time conditions. They can readily incorporate up-to-the-minute traffic information, automatically rerouting technicians around sudden delays or congestion. This dynamic rerouting feature can lead to significant time savings, especially in urban areas with unpredictable traffic patterns. It has been observed that these kinds of rerouting adjustments can reduce overall travel time by up to 30%.
Another area where these tools shine is in the use of predictive analytics. By analyzing past travel patterns, service request frequency, and other relevant data, including seasonal variations, the software can anticipate future service demands and proactively optimize schedules. This helps ensure technicians are in the right place at the right time, minimizing idle time and improving overall resource utilization.
Furthermore, advanced route optimization software has proven remarkably effective in optimizing multi-stop routes. The ability to intelligently sequence service calls can dramatically reduce overall travel distance. Research suggests that incorporating this real-time multi-stop optimization can, on average, reduce total distance traveled by around 20%.
It's interesting to note how the integration of geofencing technology enhances these tools. Geofencing allows the software to create virtual boundaries around service locations and alert technicians when they approach. This automated notification system helps technicians stay organized and helps them avoid spending time on unnecessary preparation. This integration of location tracking and notifications eliminates a fair amount of time spent looking for addresses or preparing for work at the wrong site.
The increased integration of Internet of Things (IoT) devices into vehicles and equipment also helps optimize routes and enhances their capabilities. IoT sensors can collect real-time data on vehicle location and speed. This data can then be used by the routing software to generate even more accurate estimated arrival times. Improved accuracy in estimated arrival times, in turn, helps improve communications with customers and enhance their experience.
Route optimization systems are also becoming more capable of factoring in environmental conditions. Factors like adverse weather or unexpected road closures can be readily integrated into the route planning process. This capability is important for optimizing routes, ensuring safety, and delivering timely service in any conditions. The capability of the software to analyze data relating to weather, road closures, and other unexpected conditions can be quite handy for improving the safety of field technicians.
Modern route optimization solutions often come equipped with user-friendly mobile applications, providing technicians with convenient access to routes on-the-go. Even if the technicians experience areas without strong network connections, they can still access these routes readily, improving overall workflow.
These systems also offer a level of customization to tailor the routing process to specific operational needs. Users can often specify preferences for vehicle types, preferred travel times, or specific service requirements. This ability to configure the parameters ensures the routing recommendations are aligned with operational goals and constraints.
Moreover, the synergy between advanced route optimization software and AI-powered scheduling systems is noteworthy. By integrating the two, businesses can create a unified and efficient workflow that combines optimized travel routes with intelligent scheduling. This seamless integration can result in faster response times and reduced delays.
Finally, the use of data collected by these systems can be used to continually refine workflows and eliminate inefficiencies. The collected data, including historical information on travel times, delays, and technician performance, allows for more effective planning and improves the software over time. Analyzing this data can reveal subtle but important patterns that can help optimize routes and procedures even further.
By embracing these sophisticated route optimization technologies, field service organizations are well-positioned to enhance their operational efficiency and deliver service more effectively. It appears these tools not only optimize routes, but can also lead to tangible improvements in overall service delivery and customer experience.
More Posts from zdnetinside.com: